|
Наши проекты
Ветераны
Мы были как все, нас война изменила...
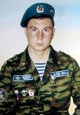
Боевики были всего в трёх метрах, так близко, что я слышал их смех, издёвки, подколы, было очень страшно. Комбат по рации огонь артиллерии на себя стал вызывать, а я в какой-то момент не выдержал, и решил покончить с собой, лучше смерть, чем плен. Спасла артиллерия. Снаряды артиллеристов попридержали "духов", у меня возродилась надежда, я пришёл в себя, воспрянул, снова стал стрелять по боевикам. Когда погибли Доставалов и Евтюхин, я пересчитал свои оставшиеся боеприпасы, оказалось - 6 патронов... Романов, вставив последний рожок с патронами в автомат, сказал: "Кто-то должен выжить и рассказать о нас правду. Уходите, пацаны, я вас прикрою"...
Портные «особого назначения»
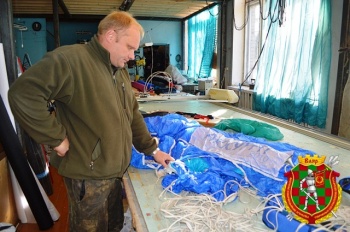
…Серия гулких коротких сигналов заставила подняться со своих мест около сотни двадцатилетних парней. Спустя несколько секунд рёв двигателей «Ильюши» приглушил новый звук — протяжный гудок сирены. В это же время открылась грузовая рампа самолёта. По команде старшего ребята один за другим устремились в объятия «пятого океана». И это при скорости самолёта 350 километров в час!
Чтобы доверить свою жизнь куску белой материи, нужно быть невероятно мужественным человеком — не так ли? А сколько необходимо иметь внутренних сил, решительности и отваги, чтобы самому шить парашюты, тем самым беря на себя ответственность за чужие жизни?..
От коллег я узнал о том, что в нашей стране есть мастерская, в которой изготавливаются парашюты, — единственная в Беларуси. Находится она в Витебске.
С многочисленными вопросами к портным «особого назначения» я отправился в северную столицу…
— Идея заниматься изготовлением парашютной техники возникла у меня тринадцать лет назад, — рассказал в своем кабинете директор мастерской Сергей Насатович. — Конечно, технологически в пошиве тех или иных изделий ничего нового мы не придумали — за основу взяли лекала уже существующих современных парашютных систем.
В первые несколько лет мастерская под началом Сергея Викторовича выпускала лишь специальные комбинезоны и парашютные ранцы для сборных команд областных клубов ДОСААФ нашей страны по парашютному спорту. Следующим шагом в развитии производства стал пошив парапланов и кайтов.
Для тех, кто не знает, поясню: кайт — это своеобразный воздушный змей, предназначенный для буксировки человека. Изготавливается он в виде небольшого паруса. В готовом виде кайт прикрепляется стропами к специальной планке, которую спортсмен держит в руках. С его помощью можно кататься на лыжах и сноуборде, а также по воде на специальной доске.
Как рассказал Сергей Викторович Насатович, весь коллектив мастерской, прежде чем приступить к пошиву парашютных систем, прошел обучение в Иркутском научно-исследовательском институте парашютостроения. Там около двух месяцев наши земляки изучали процесс разработки и изготовления перспективных парашютных систем различного назначения.
Сегодня витебские портные способны самостоятельно разрабатывать и изготавливать почти все типы современных парашютных систем: спасательные, десантные, спортивно-тренировочные, посадочные тормозные, для беспилотных аппаратов, низковысотного десантирования, для авиационных и артиллерийских боеприпасов…
Для пошива парашютов в Витебске ткань закупают во Франции, стропы — в Германии, нити — в Англии. Самый первый изготовленный в мастерской Сергея Насатовича парашют портной проверял в деле сам…
Испытания первой отшитой здесь партии проходили в два этапа. Сначала из самолета на высоте в 400 метров был выброшен парашют с манекеном человека.
— Он раскрылся с первого раза! — с гордостью вспоминает сегодня Сергей Викторович, — Конечно, ныне чувства, которые я испытывал в то мгновение, передать уже трудно… Когда мы решились на вторую часть эксперимента — десантирование людей, я принял решение: сам первым совершу прыжок. Как видите, приземлился благополучно.
Примечательно и то, что для Сергея Насатовича тот прыжок был далеко не первым. Он мастер парашютного спорта СССР. Сегодня на его счету более 3.000 прыжков с парашютом, часть из них Сергей Викторович совершил на «своих» парашютных системах.
Потом был еще не один день испытаний. Первую партию парашютов, отшитую витебскими мастерами, проверяли с особым пристрастием. Было сделано около 2.000 прыжков на каждом парашюте. Причем 200 из них были специальные: с завязыванием или перекручиванием строп, порывом материи…
* * *
Стоит отметить, что в испытаниях некоторых типов парашютных систем, изготовленных витебчанами, принимали участие и военнослужащие наших сил специальных операций.
Как рассказал мне по телефону старший тренер команды Вооруженных Сил по парашютному спорту старший прапорщик Михаил Карпов, в рамках проведения подконтрольно-эксплуатационных сборов нашими армейскими спортсменами были испытаны парашютные системы типа П1‑У и «Аккурат‑2010».
— Во всех проведенных нами испытаниях данные типы парашютных систем показали себя очень хорошо. В нашей команде по парашютному спорту пятая часть мужской и женской сборных тренируется и выступает на этих парашютных системах, — отметил Михаил Леонидович. — «Аккурат‑2010» используется нами в тех состязаниях, где важна точность приземления спортсмена. А запасной парашют этой же системы мы эксплуатируем во время отработки групповой акробатики.
По словам старшего прапорщика Михаила Карпова, только в этом году на данной парашютной системе он совершил 350 прыжков (всего у Михаила Леонидовича их около 9.000).
Интересен и тот факт, что армейские спортсмены, выступая на различных состязаниях, заработали немало наград, используя парашютную систему, пошитую нашими земляками. Так, на 39‑м чемпионате мира по парашютному спорту, который проходил в октябре этого года в Республике Корея, наша мужская сборная стала победителем в командной точности по приземлению.
«Спасибо за парашют!» — такую надпись в специальных рамках, размещенных на стенах, можно встретить в этой мастерской: она — от благодарных спортсменов‑парашютистов. Немало таких же благодарностей здесь и от армейцев. Одна из последних — от спортсмена-инструктора взвода воздушно-десантной подготовки командования сил специальных операций Вооруженных Сил Беларуси мастера спорта международного класса по парашютному спорту старшего сержанта Антона Гуриновича.
— Армейские спортсмены — частые гости на нашем производстве, — подчеркнул Сергей Насатович. — У нас очень дружные отношения со сборной по парашютному спорту нашей 103‑й гвардейской отдельной мобильной бригады. И многие военные пенсионеры до сих пор совершают прыжки — уже в составе команд аэроклубов ДОСААФ нашей страны.
* * *
А в производственном цеху Сергей Викторович поведал о том, что пошив купола парашюта начинается с изготовления прочной нейлоновой ткани со специальными нейлоновыми вплетениями.
— На специальном световом столе швея располагает ткань так, чтобы можно было увидеть все ее дефекты, — пояснил помощник начальника мастерской по производственной части Максим Зверев. — Затем материал натягивают до момента его разрыва. Согласно требованиям, предъявляемым к «парашютине», автоматическая установка создает натяжение в 20 килограммов. Если материя рвется при меньшей нагрузке, ее отправляют обратно поставщику.
После теста на прочность ткань собирают и раскладывают на новом столе. Там ее вновь натягивают и закрепляют. Потом в работу вступает специальный лазер. Он в зависимости от модели парашюта выкраивает от 30 до 100 штук его деталей. Вакуумное устройство прижимает материю в процессе раскроя к столу.
Купола парашютов изготавливают совершенно разными по цвету. В витебской мастерской можно увидеть будущие купола из материи красных, желтых, синих и даже серебряных оттенков.
— После того как ко мне поступают уже кадрированные части будущего купола парашюта, я прострачиваю края нейлоновой лентой, — рассказала швея Ирина Котляренко. — Некоторые купола сшиваются таким образом, чтобы между отдельными частями были отверстия (примерно 40 сантиметров). Служат они для того, чтобы пропускать воздух между двумя слоями купола и поддерживать его жесткость во время полета.
Как только швея заканчивает сшивать купол парашюта, помощник начальника мастерской по производственной части Максим Зверев проверяет качество швов.
— На каждых двух с половиной сантиметра шва должно быть от семи до десяти стежков, — уточнил Максим Николаевич. — Если стежки мелкие или слишком большие, материал во время снижения парашютиста может порваться.
Когда качество швов проверено, следующая работница мастерской нашивает нейлоновую ленту. Делается это для того, чтобы укрепить участок сшивки, который профессионалы называют «клин».
Выглядит «клин» в форме треугольной накладки. Он изготовлен из нейлона и пропитан слоем силикона. Швея делает из ленты петлю на одном из концов «клина», чтобы потом продеть в нее так называемую стропу. 60 строп соединяют 60 клиньев купола с подвесной системой парашютиста. Чтобы укрепить каждый клин, машинкой делают 42 зигзагообразных шва на участке в два с половиной сантиметра.
Стропы парашюта изготавливают следующим образом. Рабочий отмеряет 4,5 метра каждого шнура и отрезает его под углом, чтобы он не расплетался. Затем портные сшивают концы в петле, чтобы каждую можно было прикрепить к петле на клиньях. Каждая стропа крепится к «клину» специальным морским узлом. Такой узел легко развязать, если стропа требует замены, но при натяжении он еще больше затягивается.
Чтобы прикрепить 60 строп к 60 клиньям купола, требуется около двух часов. Только после того как все узлы закреплены, парашют укладывают в ранец и отправляют заказчику.
Источник: Белорусская военная газета «Во славу Родины», выпуск № 213
Автор новости: Игорь Деменков, фото автора

